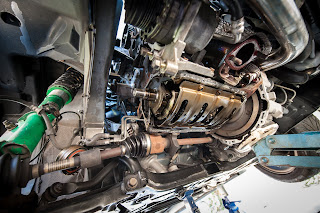
Some previous photos of a bottom end>>
So we already hit a snag when i picked up the wrong sheet and was torquing the bolts down to 80ftlb (~111Nm) instead of the 60ftlb (84Nm). Looks like the boxes got switched. Fun times :(
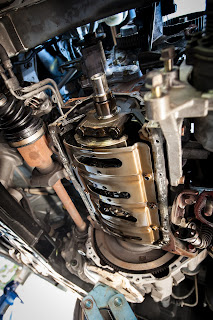
11mm bolts run a 82ftlb rating (200,000PSI).
The box has a bunch of spare bolts, i think because in the Evo the main caps/cradles use bolts.
So I started by washing the block down with detergent and give it a good clean.
Air compressor drying and sprayed it with CRC (I didn't have my WD40 on me).
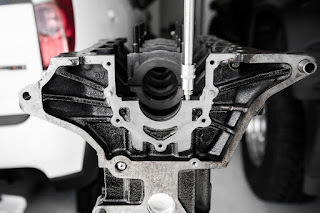
I ran a thread chaser down all the main cap threads M10x1.25. I found that when spinning them in hand tight they all didn't bottom out the same.
I cleaned all bearing caps, I used some kerosene. Good and removing oil deposits. I seen builders use Brake Kleen.
I believe the front cap (cap 1) uses bolts and not studs. Studs are a lot stronger, i believe it could be due clearance?
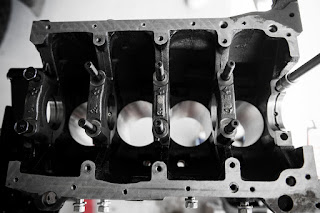
Thread cleaning and installing studs
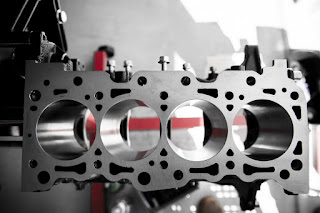
Cleaning and measuring
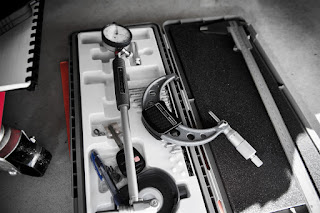
Ouch
I should have realised earlier, M10 run about 60ftlbs. But I guess when i saw the paper with 85, I just thought wow ok. Here we go :(
Due to this over torque, I may have over stretched them. I will conduct close measurements. ARPs are not meant to stay stretched unless you exceed their elastic limit and they won't stretch
Some of the tools i bought earlier - /tools-percision-instruments.html
ARP Sites -
Main - /instructions/207-5401.pdf
Head - /miata-arp-head-studs/
Head Bolts - /instructions/201-4302.pdf
(This is oversized M10, OEM head studs are 9mm)
My next set of plans is to clean the crank, measure the journals, redo the main caps, work out oil clearances for the bearings and install the crank. I will also attempt to measure crank walk. I didn't buy a magnetic stand, so i was planning to use feeler gauges.
After crank is installed i will re-measure the bores, pistons and start working on ring gaps and big end oil clearances.
Installation Extracts: /SBC_Main_Studs_Installation.pdf
STUDS vs. BOLTS
ARP® recommends the use of main studs over bolts whenever possible for several key
reasons. First is the ability to obtain more accurate torque readings because studs don’t
“twist” into the block. All clamping forces are on one axis. By the same token, there is
less force exerted on the block threads, which contributes to improved block life
(very critical on aluminum blocks). Finally, there are factors of easier engine assembly
and proper alignment of caps every time.
Install
There are a number of important considerations when installing ARP® main studs. First and
foremost is making sure the block and studs are as clean as possible. Foreign matter and debris can easily affect the quality of thread engagement and cause erroneous torque readings. Do not re-cut threads in the block—use the special “chaser” taps as listed on page 80 of this catalog. This will preserve the integrity of the threads and provide better engagement. You should also make sure your torque wrench has been calibrated. Even new wrenches have been known to be off by as much as 10 foot pounds!
Use consistent tightening techniques.
1. Clean and chase appropriate threads in block to ensure proper thread engagement and
accurate torque readings.
2. All hardware (and caps) should be cleaned and inspected prior to installation, looking for any shipping damage or defects.
3. Screw studs into block, finger tight ONLY. For permanent installation, apply Loc-tite (or similar adhesive) sparingly to threads. Be sure and install the caps promptly before the cement sets to prevent misalignment of studs in block.
4. Install main caps, checking for binding and misalignment. Lubricate threads, nuts and washers with oil or ARP® moly assembly lubricant before installation. Note that torque specs will vary by lubricant. Moly lube is most consistent. Have block align honed.
5. Using the instructions provided with the studs, tighten the nuts to proper torque values three times. NOTE: If using Loc-Tite or similar cement, proper preload must be achieved prior to it setting up